Ontwerpen met Roestvast Staal
Roestvast staal is niet moeilijker te bewerken dan koolstofstaal, het is alleen anders. Het zich bewust zijn van de fysische en mechanische eigenschappen stelt de ontwerper in staat om profijt te trekken van de vele mogelijkheden die roestvast staal biedt, zoals hoge sterkte, hoog spiegelend vermogen en uitstekende reinigbaarheid, om er enkele te noemen.
A.J. Schornagel
De diverse soorten roestvast staal bieden de ontwerpvoordelen zoals:
- uitstekende corrosieweerstand;
- hoge sterkte;
- hoge stijfheid;
- hoge weerstand tegen natte abrasie;
- vermogen om te werken van cryogene tot hoge temperaturen;
- goede vervormbaarheid;
- goede lasbaarheid;
- uitstekende reinigbaarheid en hygiënische eigenschappen.
Roestvast staal is leverbaar met tal van oppervlakteafwerkingen.
Roestvast-staalgroepen
De term roestvast staal dekt een familie van chroomhoudende legeringen, waarvan elk zijn specifieke eigenschappen bezit.De familie kan worden verdeeld in ondergroepen op grond van hun microstructuur:
- austenitisch;
- ferritisch;
- duplex (ferritisch-austenitisch);
- martensitisch;
- precipitatiehardend (PH).
Austenitisch roestvast staal
De meest gebruikte austenitisch typen zijn 304 en 316. Een relatief hoog nikkelgehalte geeft een volledig austenitische microstructuur, die zorgt voor betere vervormbaarheid, taaiheid, kerfslagsterkte en lasbaarheid. Andere elementen zoals molybdeen en titanium worden wel toegevoegd voor additionele eigenschappen. Molybdeen verbetert de weerstand tegen lokale corrosie, zoals spleetcorrosie en putcorrosie, doordat het de passieve laag stabieler maakt. Titaan kan sensitisering en interkristallijne corrosie voorkomen.
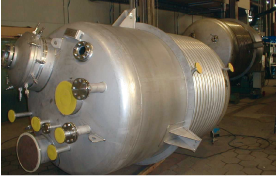
Een Hastelloy C276-reactorvat, SRI Veenwoude.
Typische toepassingen voor austenitisch roestvast staal zijn:
- huishoudelijke voorwerpen;
- commerciële keukenapparatuur;
- treinwagons;
- industriële voedingsverwerkende apparatuur;
- apparatuur en installaties voor de chemische en procesindustrie;
- drukvaten;
- opslagtanks.
Bedrijfscondities
Alvorens materiaal te kiezen, dient er een grondige analyse plaats te hebben van de te verwachten bedrijfsomstandigheden. Er zijn een aantal factoren die de agressiviteit van een milieu bepalen.
Afbeelding 1. Isocorrosie-diagram voor zwavelzuur.
De ontwerpspecificaties dienen zaken te dekken zoals:
- Chemische samenstelling van het milieu, inclusief type en concentratie van eventuele verontreinigingen.
- Werkingscondities zoals maximum en minimum temperaturen (hogere temperatuur kan een hoger gelegeerd RVS-type vereisen, zoals is te zien op afbeelding 1, het isocorrosie-diagram voor zwavelzuur).
Afhankelijk van de toepassing, moeten de ontwerpspecificaties ook rekening houden met zaken als:
- Te verwachten stromingscondities, stilstand kan leiden tot microbiologisch beïnvloede corrosie en neerslagen kunnen resulteren in spleetcorrosie. - Afwisselend of continu gebruik. - Stromingssnelheid, hardheid, afmetingen en verdeling van zwevende deeltjes die kunnen leiden tot erosie corrosie.
- Te verwachten spanningscondities. Statische spanningen kunnen leiden tot scheurvormende spanningscorrosie of beïnvloeding van het kruipgedrag, terwijl dynamische spanningen vermoeiingscorrosie of vermoeiing kunnen opwekken. Lasconfiguraties kunnen ook verder spanningen induceren.
Er dient in het bijzonder aandacht worden geschonken aan de waarschijnlijkheid van enige vorm van korte termijn variaties die optreden in de heersende temperatuur, druk of concentratie. Deze variaties kunnen ernstige gevolgen hebben en dienen zoveel mogelijk te worden voorkomen.
Selectiefactoren
Als de bedrijfsomstandigheden eenmaal zijn bepaald, dan kan het geschikte type roestvast staal worden gekozen. Er zijn een aantal factoren die in ogenschouw moeten worden genomen bij de keuze van een materiaal voor het ontwerp van een bepaald onderdeel:
- Corrosieweerstand. Kies een type met geschikte corrosieweerstand voor de toepassing, milieu en onderhoud.
- Mechanische eigenschappen zoals treksterkte, vermoeiingssterkte, kruipweerstand en kerfslagsterkte.
- Bewerkingskarakteristieken zoals lasbaarheid, vervormingseigenschappen en verspaanbaarheid.
- Economische overwegingen zoals prijs en leverbaarheid.
Weerstand tegen het milieu
De weerstand van roestvast staal tegen een bepaald milieu hangt af van het type en de concentraties van aanwezige stoffen, temperatuur en verblijftijd. bestaat een overvloed aan corrosiegegevens, maar de meerderheid van deze gegevens is afkomstig van laboratoria waar ze zijn bepaald onder goed gedefinieerde omstandigheden, die lang niet altijd de complexiteit van de feitelijke werkingscondities representeren. Zulke gegevens (tabellen, isocorrosiediagrammen, kritisch putcorrosie-diagrammen, enzovoort) dienen daarom alleen als richtlijn te worden gebruikt.
Tabel 1. Eigenschappen van enkele staalsoorten
Materiaal | Eigenschappen | ||||
---|---|---|---|---|---|
Rp0,2, MPa |
Rm, MPa |
Rek, % |
Thermische uitzetting, (0-100oC) |
Warmtegeleiding, W/moC bij 200oC |
|
Austenitisch | 270 | 650 | 57 | 16 | 15 |
Duplex | 500 | 750 | 35 | 13 | 15 |
Ferritisch | 325 | 515 | 28 | 10 | 25 |
Martensitisch | 600 | 800 | 10 | 10,5 | 30 |
PH | 1000 | 1070 | 12 | 10,9 | 16 |
Koolstofstaal | 300 | 430 | 25 | 11,3 | 49 |
Tabel 2. PRE-waarden van een aantal staaltypen.
Groep | Type | Cr | Mo | N | PRE |
---|---|---|---|---|---|
Austenitisch | 304 | 18,5 | - | - | 19 |
Austenitisch | 316 | 17,0 | 2,1 | - | 24 |
Austenitisch | 254SMO | 20,0 | 6,0 | 0,2 | 43 |
Ferritisch | 409 | 11,5 | - | - | 12 |
Ferritisch | 430 | 17,0 | - | - | 17 |
Ferritisch | 444 | 18,5 | 2,0 | - | 25 |
Duplex | 2101 | 21,5 | - | 0,22 | 25 |
Duplex | 2205 | 22,0 | 3,0 | 0,14 | 34 |
Er bestaat een overvloed aan corrosiegegevens, maar de meerderheid van deze gegevens is afkomstig van laboratoria waar ze zijn bepaald onder goed gedefinieerde omstandigheden, die lang niet altijd de complexiteit van de feitelijke werkingscondities representeren. Zulke gegevens (tabellen, isocorrosiediagrammen, kritisch putcorrosie-diagrammen, enzovoort) dienen daarom alleen als richtlijn te worden gebruikt. De beste methode om uit te maken of een materiaal geschikt is voor een bepaalde toepassing is het uitvoeren van proeven in het milieu in de fabriek of installatie zelf. Dit is echter lang niet altijd mogelijk en daarom is het van belang om inzicht te hebben in de corrosietypen die in verschillende milieus kunnen worden verwacht. Naast de verschillen tussen de verscheidene RVSsoorten en -typen, is het noodzakelijk om begrip te hebben van de verschillen tussen de RVS-soorten en andere ferro-legeringen zoals koolstofstaal, zie tabel 1.
Corrosieweerstand
Roestvast staal wordt het vaakst geselecteerd ter verzekering van de duurzaamheid van constructies. Dit is met name het geval in agressieve of corrosieve milieus waar ander materiaal snel kan worden aangetast. Als gevolg hiervan wordt roestvast staal vaak gebruikt voor veeleisende toepassingen. Het kiezen van het juiste roestvast staal voor een toepassing vormt een deel van de verzekering van duurzaamheid, maar er zijn ook nog andere ontwerpaspecten die aandacht eisen ter vermijding van corrosie.
Put- en spleetcorrosie
Put- en spleetcorrosie zijn de meest voorkomende corrosiemechanismen die optreden bij roestvast staal. Ze kunnen vaak worden vermeden door middel van goed ontwerpen. Kies een materiaal met hoge weerstand tegen putcorrosie. Verhoging van het gehalte aan Cr, Mo en N verbetert de weerstand tegen putcorrosie. Hierbij kan gebruik worden gemaakt van de PRE (Pitting Resistance Equivalent), die kan worden gevonden met de empirische formule: PRE = %Cr + 3,3%Mo + 16%N Aan de hand van de gevonden PRE-waarden kan er een rangschikking worden gemaakt, waarbij geldt dat hoe hoger de PRE des te hoger de weerstand tegen putcorrosie. Tabel 2 geeft de PRE-waarden van een aantal RVS-soorten en -typen. Voorts is het van belang om een geschikte oppervlakte afwerking te kiezen, waarbij geldt dat hoe gladder het oppervlak, des hoger de corrosieweerstand.
Afbeelding 2. Tanks en vaten dienen zodanig te worden ontworpen, dat ze geheel kunnen worden geledigd.
Voorbeelden van basis-ontwerpprincipes om putcorrosie te helpen vermijden zijn:
- Ontwerp zodanig dat lediging mogelijk is om opzameling van vloeistof tegen te gaan, zie afbeelding 2.
- Ontwerp zodanig dat er geen verdamping en condensatie kan optreden die hoge concentraties van corrosieve stoffen, zoals chloriden, kunnen veroorzaken.
- Verhoog daar waar mogelijk de stroomsnelheid van het corrosieve milieu.
Voorbeelden van basis-ontwerpprincipes om spleetcorrosie te vermijden zijn:
- Vermijd in het ontwerp nauwe spleten, scherpe hoeken waar vaste stoffen zich kunnen opzamelen.
- Pas gelaste verbindingen toe in plaats van boutverbindingen om spleten te vermijden die ter plaatse van de overlap kunnen ontstaan.
- Vermijd bij kritische toepassingen het gebruik van plaketiketten, verf, markeerstiften, enzovoort, die even zovele spleten kunnen opleveren.
- Kies een type met voldoende corrosieweerstand voor de toepassing, milieu en onderhoud.
Spleetcorrosie
- Ontwerp zodanig dat er sprake is van totale lediging.
- Gebruik niet-absorberend pakkingmateriaal.
- Verwijder tijdens bedrijfsstops pakkingmateriaal en sediment.
Als spleten niet zijn te vermijden kies dan een hoger gelegeerd type. Spleetcorrosie treedt bij lagere temperaturen op dan putcorrosie, zo’n 20°C lager. Het verschil tussen de starttemperatuur voor putcorrosie en voor spleetcorrosie stijgt voor de hoger gelegeerde staalsoorten.
Scheurvormende spanningscorrosie
Scheurvormende spanningscorrosie (SSC) is het gevolg van het gecombineerde effect van een agressief ion (meestal het chloride-ion), trekspanningen en temperatuur. SSC doet zich het meest voor bij de gewone austenitische typen zoals 304 en 316. SSC kan worden vermeden door een of meer van deze voorwaarden weg te nemen:
- Kies voldoende resistent materiaal, bijvoorbeeld een duplex of super ferritisch type of austenitische RVS-typen met een hoog (>25%Ni) gehalte.
- Zorg indien mogelijk voor een chloride vrij milieu.
- Beperk trekspanningen tot een laag niveau dat wil zeggen onder de drempelspanning voor SSC. Dit kan lastig zijn omdat er spanningen aanwezig kunnen zijn die het gevolg zijn van het fabricageproces.
- Kies lagere bedrijfstemperaturen. SSC treedt op boven 50°C.
- Pas inhibitoren of kathodische bescherming toe.
Microbiologisch beïnvloede corrosie
Microbiologisch beïnvloede corrosie kan als volgt worden bestreden:
- Maak gebruik van behandeld water (gechloreerd of behandeld met ozon, enz.) voor hydrostatische beproeving, gebruik geen natuurlijk water.
- Houd het water in circulatie, tap af en droog direct na beëindiging van hydrostatische beproeving.
- Gebruik biociden.
- Kies materiaal met hogere corrosieweerstand.
Corrosie bij hoge temperaturen
In oxiderende milieus en bij matig verhoogde temperaturen, zal zich een oxide vormen, dat zelfs in aanwezigheid van zwavel, bescherming biedt. Bij hogere temperaturen (>850°C) kan de oxidelaag openbreken hetgeen gepaard gaat met een plotselinge toename van de scaling (vorming van een niet-beschermend vrij poresu oxide). Er staan speciale hoge-temperatuur typen ter beschikking zoals 309, 310, 446, 253MA en 353MA.
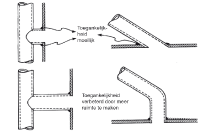
Afbeelding 3. Ontwerp zodanig dat de lasser erbij kan.
Afbeelding 4. Gebruik ondoordringbaar afdichtmateriaal voor het afdichten van spleten in boutverbindingen.
Oxidatie
Oxidatie is de gebruikelijke vorm van hoge-temperatuur corrosie. Bij isotherm gebruik hangt de oxidatieweerstand van roestvast staal af van het chroomgehalte. Typen met minder dan 18% Cr zijn bruikbaar tot ongeveer 800°C, typen met 18-20% Cr zijn te gebruiken tot 920°C en die met zo’n 25% Cr boven 1100°C. Vaak zijn de gebruiksomstandigheden niet isotherm en doet zich afsplijting van de oxidehuid voor als gevolg van uitzetting en inkrimping. Toevoeging van Ni aan het staal verbetert de weerstand tegen dit afsplijten, omdat de verschillen tussen de uitzettingscoëfficiënten van oxide en metaal worden verminderd. Verontreinigingen in de vorm van S, H2S, Na, V, Cl- versnellen de corrosie.
Ontwerpen van verbindingen
In geval van lasverbindingen dient er in het ontwerp rekening te worden gehouden met goede toegankelijkheid voor de lasser(s) alsmede de benodigde apparatuur, afbeelding 3. De lassen zelf moeten volledig zijn doorgelast om spleten en daarmee spleetcorrosie te voorkomen. Hoewel volledig gelaste constructies de voorkeur hebben, kan het nodig zijn om toch gebruik te maken van boutverbindingen. In dat geval moeten de spleten tussen overlappende delen worden afgedicht met een ondoordringbaar mastiek afdichtmiddel of een samendrukbare pakking, afbeelding 4.
Economisch ontwerpen
Een ontwerp dient niet alleen efficiënt te zijn, maar ook economisch. In die zin is het voordelig om gebruik te maken van beschikbare plaatdiktes en plaatafmetingen. Door de fysieke afmetingen van bijvoorbeeld een vat af te stemmen op de beschikbaarheid van een materiaal en de afmetingen waarin het geleverd wordt, kunnen aanzienlijke voordelen worden behaald. Als een drukvat wordt gespecificeerd, wordt gewoonlijk de volgende informatie gegeven:
- ontwerptemperatuur;
- ontwerpdruk;
- diameter en andere afmetingen.
Afbeelding 5. Verband tussen wanddikte en diameter voor verscheidene drukniveaus.
Afbeelding 6. Verloop van de toelaatbare spanning als functie van de temperatuur.
Al deze aspecten zijn direct van invloed op de vereiste wanddikte van het vat en, door enkele ervan aan te passen, kan er gebruik worden gemaakt van standaard plaatafmetingen.
Ontwerpdruk en -temperatuur
Deze waarden worden onveranderlijk ontleend aan de procesomstandigheden die in het vat optreden. Beide zijn direct van invloed op de vereiste wanddikte. Als of de temperatuur, of de druk worden verhoogd, moet de wanddikte ook worden verhoogd. Een verhoging van de bedrijfstemperatuur verlaagt de toelaatbare maximum spanningen voor het materiaal in kwestie (zie afbeeldingen 5 en 6). Het is daarom van belang dat de werkdruk en -temperatuur, alsmede de ontwerptemperatuur niet overgespecificeerd worden.
Afmetingen van het vat
De diameter en omtrek van het vat worden bepaald door het volume van de stof die er in moet. Er geldt een standaard omtrek/diameter verhouding van 2:1. Als de vereiste diameter is bepaald, waarbij wordt afgerond op vijftigtallen (bijv. 638 mm wordt 650 mm), ligt de omtrek vast die nodig is om het gespecificeerde volume plaats te kunnen bieden. Om optimaal gebruik te maken van standaard plaatafmetingen, kan de diameter worden aangepast. Bijvoorbeeld een vat met een diameter van 1.000 mm vereist een plaat met een lengte van 3.142 mm, wat geen standaard maat is. Door nu de diameter terug te brengen tot 955 mm, kan er een standaard plaat van 3.000 mm lengte worden gebruikt. De significante extra kosten om een extra strook staal aan het einde van een standaard plaat te lassen om de lengte op 3.142 mm te brengen worden aldus vermeden. Het is net zo belangrijk om (aan de hand van voor dit doel beschikbare tabellen) een materiaaldikte te kiezen die standaard is. Plaatdikten worden bepaald door de diameter en inwendige druk van dat vat. Een voorbeeld van overspecificeren van de dikte is waar ontwerpberekeningen aangeven dat er bijvoorbeeld 6,5 mm dik staal moet worden gebruikt. De dichtst bij gelegen standaarddikte is 0,8 mm dikker, een toename van 25% aan onnodig materiaal en dus extra kosten. Om het gebruik van materiaal te optimaliseren en om fabricagekosten te verlagen, kunnen de afmetingen van een vat worden bepaald door de maximaal toelaatbare diameter van het vat te berekenen met onderstaande formule:
R = t(SE - 0,6P)/P
waar:
t = vereiste minimum wanddikte
P = (ontwerpdruk)/(maximum toelaatbare werkdruk)
R = inwendige vatdiameter
S = maximum toelaatbare spanningswaarde
E = efficiëntie van de verbinding
Hoewel deze methode om de plaatdikte/vatdiameter te bepalen resulteert in wat afsnijwerk, is het afsnijden van een stuk materiaal te prefereren boven het aanbrengen van betrekkelijk kleine stukken ter verlenging van een plaat. Afgesneden stukken plaat kunnen worden gebruikt voor bijvoorbeeld steunen, hijsplaten, verstevigingsribben, enzovoort, terwijl het aanbrengen van extra materiaal alleen maar tijdverslindend en duur is.