Oppervlaktebehandeling van werkstukken uit magnesium en legeringen
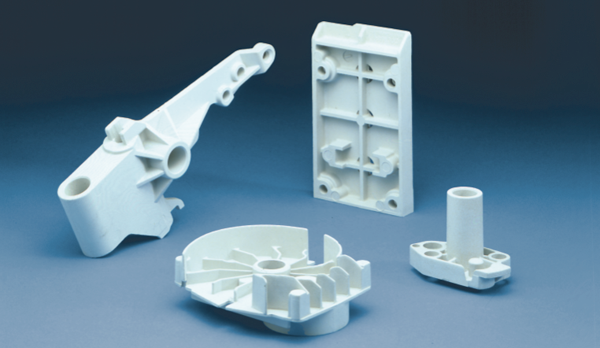
Het lichtmetaal magnesium wordt meer en meer ingezet als constructiemateriaal. Goede oppervlaktebehandelingen, met een relatief gering aandeel in de kostprijs van het eindproduct, kunnen de kwaliteit van producten uit dit metaal of legeringen daarvan sterk verhogen.
Hans Koopmans
Magnesium is van alle constructiematerialen op afstand het lichtste metaal. De soortelijke dichtheid van aluminium bedraagt nog altijd 2,7 g/cm³; voor magnesium ligt die waarde op slechts 1,74 g/cm³. Door legeringselementen zoals aluminium, mangaan, zink enz. (met een aandeel tot ca. 10%) kan de sterkte verder worden opgevoerd. Magnesiumlegeringen worden overwegend verwerkt in zand-, coquille- en spuitgietprocessen. en als kneedlegeringen. Het meest gebruikelijk zijn de spuitgietlegeringen, waarvan de zeer zuivere legering AZ91HP, mede vanwege de goede mechanische eigenschappen en uitstekende gietbaarheid, het meest wordt toegepast. De weerstand tegen corrosie ligt bij dit type op een hoog niveau. Op dit punt is AZ91HP vergelijkbaar met aluminiumlegeringen zoals GD-AlSi9Cu3.
Toepassingen
Het zijn de lage smelttemperatuur, de geringe smeltenergie en warmtecapaciteit die magnesium(-legeringen) zo geschikt maken - geschikter dan aluminium - voor het spuitgietproces. Ook reageert gesmolten magnesium niet met ijzer uit de matrijs. Van groot belang is het gegeven, dat dunwandige onderdelen met nauwe toleranties kunnen worden gegoten. Bij verspanen zijn aanzienlijk lagere snijkrachten nodig dan bij andere metalen. Er ontstaan korte spanen, wat een gunstig aspect is in verband met automatische fabricage op CNC-machines. Daarbij is de gereedschapslijtage ook weer minder dan bij andere metalen. Vergelijken we magnesium op dit punt met aluminium, dan ligt de standtijd van de gereedschappen vijf tot tien maal zo hoog. Men kan daarom met 50% hogere snijsnelheden werken en waarden bereiken van 1000 tot 7500 m/min. Daarbij komt nog dat de oppervlaktekwaliteit bij het verspanen van magnesium als zeer goed beoordeeld mag worden. Gezien het voorgaande is het niet verwonderlijk dat magnesium in steeds meer industriële toepassingen en sectoren wordt verwerkt, als het gaat om een combinatie van gewichtsbeparing met uitstekende sterkte-eigenschappen. Enkele voorbeelden: de lucht- en ruimtevaart, transportmiddelenbouw, ICT, huishoudelijke apparatuur, machinebouw, levensmiddelindustrie en energietechniek. Producten als racefietsen, stuurwielen, versnellingsbakken, notebooks en camcorders worden vaak op basis van magnesiumlegeringen vervaardigd. Het ontwikkelingspotentiaal van magnesium is nog lang niet uitgeput, noch wat betreft de nieuwe materiaalvarianten, noch processpecifiek. De ontwikkeling gaat bij de superlichte legeringen en matrix-constructiematerialen net zo goed verder als bij de koolstofvezelversterkte Mg-legeringen, recepturen op magnesium-lithiumbasis en andere kruipvaste Mg-legeringen met een verlaagde dichtheid. Ook in de technieken voor grootserieproductie zijn innovaties te voorzien, bijvoorbeeld in de richting van het thixogieten c.q. thixovormen (vormgeving in gedeeltelijk gestolde toestand) of verwerking van magnesiumschuimen met een homogene poriënstructuur.
Oppervlakteveredeling
Hoe de toekomstige ontwikkeling van magnesiummaterialen ook zal verlopen, ze blijven op grond van hun elektrochemische eigenschappen onedel en moeten tegen corrosie worden beschermd. Bovendien moeten magnesiumoppervlakken aan talrijke functionele eisen voldoen. Verschillende door AHC, onderdeel van Aalberts Industries Material Technologies (AIMT) ontwikkelde coatingprocessen komen aan die eisen tegemoet:
- MAGOXID-COAT® (anodisch, plasmachemisch);
- MAGPASS-COAT® (chroomvrije passivering);
- GLISS-COAT® (droge coating met goede smeringseigenschappen);
- DURNI-COAT® (chemisch nikkel), m.n. de DNC-MG variant.
Anodisch aangebrachte coatings dienen niet alleen om de corrosiewerendheid te verbeteren, maar verhogen tegelijkertijd de bestandheid tegen slijtage van magnesiummaterialen
Met het anodische, plasmachemische proces MAGOXID-COAT® kunnen magnesiumlegeringen zoals AZ31, AZ61, AZ81, AZ91, AM20, AM50, AM60 en legeringen met een gehalte aan zeldzame aarde en zirkonium zoals ZE41 en WE43 worden gecoat. Het proces leidt in één stap tot een corrosievaste, goed hechtende witgrijze oxidekeramieklaag. Bij deze conversiecoating (de term ‘conversie’ geeft aan dat de bovenste laag van het basismateriaal wordt veranderd) gaat het om een kristallijn oxidekeramiek met een hoog gehalte van zeer resistente verbindingen (b.v. MgAl2O3). De coating bestaat uit een poriënarme en een poriënrijke oxidekeramische laag, opgebouwd op een sperlaag. De maximaal haalbare laagdikte hangt af van het legeringstype. Bij de legering GDMgAl9Zn1 (AZ91) worden de functionele eigenschappen (zoals corrosie- en slijtvastheid) al bij 20-30 ?m bereikt; de laagdiktetolerantie ligt daarbij op ±0,5 ?m. Magnesiummaterialen worden vaak onder zware klimatologische condities toegepast. Zout- of zwaveldioxidehoudende, vochtige lucht kan tot een sterk corrosieve belasting leiden. In dit geval fungeert de MAGOXID-COAT® niet alleen als bescherming tegen oppervlakkige corrosie en slijtage. De coating vermindert vanwege zijn elektrisch isolerende werking contactcorrosie. Een variant op de basisveredeling vormt MAGOXID-COAT® ‘zwart’. Hiermee kan op nagenoeg alle technisch belangrijke magnesiummaterialen een zwarte oxidekeramiek-coating worden aangebracht.
Passivering
MAGPASS-COAT® is een chroomvrije passivering voor magnesiummaterialen. Het proces werd door AHC ontwikkeld met als doel een equivalent voor chromaatbehandelingen aan te kunnen bieden. Door bijvoorbeeld dompelen wordt het magnesiummateriaal met de chroomvrije, anorganische waterige passiveringsoplossing behandeld. Er ontstaat een conversiecoating, die uit oxiden van de passiveringsoplossing en het basismateriaal bestaat. Alle technisch belangrijke magnesiummaterialen kunnen op deze manier behandeld worden.
De passiveerlaag wordt gelijkmatig, contourvolgend op complexe oppervlaktegeometrieën aangebracht, op kanten, in holten, reliëfs, boringen, blinde gaten enz. De MAGPASS-COAT® laag is elektrisch geleidend. Ze dient als tussenlaag voor een later aan te brengen laklaag of bekleding. Afhankelijk van de legering verschijnt de passiveerlaag in verschillende tinten van grijs tot goudbruin. De laagdikte blijft doorgaans onder 1 ?m. De belangrijkste toepassingsgebieden zijn overal te vinden waar chromaatbehandelingen moeten worden vervangen door chroomvrije systemen. De chroomvrije passiveerlaag alleen dient als tijdelijke bescherming tegen corrosie en ter verbetering van de hechting en weerstand tegen klimatologische omstandigheden van lakken. In een combi-systeem met een aansluitende lakbehandeling levert de laag een bijdrage aan de bescherming tegen corrosie van constructieonderdelen. De passiveerbehandeling vindt o.a. toepassing in sectoren als de automobielindustrie, de fietsenfabricage, de algemene machinebouw, de elektrotechniek, de luchten ruimtevaart en de telecommunicatie.
Vermindering van slijtage en wrijving
Met de naam GLISS-COAT® worden de door AHC ontwikkelde droogsmerende glijcoatings voor vermindering van wrijving en slijtage aangeduid. De coating-materialen zijn wateroplossend en kunnen volgens verschillende processen worden aangebracht. Deze processen zijn afgestemd op de geometrie en de seriegrootte, de eigenschappen van de vloeibare coating-materialen (b.v. één- of meercomponentensysteem) en de eisen die aan de gerealiseerde coating worden gesteld. Onderdelen in enkelstuksproductie worden door inzet van geautomatiseerde vlaksproeiinstallaties gecoat, terwijl kleine onderdelen in massaproductie bijvoorbeeld in speciale trommels behandeld worden. De meeste GLISS-COAT®-coatings moeten na het aanbrengen op het werkstukoppervlak gedroogd worden, opdat de systemen de gewenste eigenschappen met het oog op hechting, hardheid, corrosiewerendheid en smering verkrijgen. Een variant vormt GLISS-COAT® 2000; deze is bijzonder geschikt als bescherming tegen slijtage onder een hoge drukbelasting. Door gebruik te maken van anodische tussenlagen (bijvoorbeeld MAGOXID-COAT®) kan een optimaal wrijvingsgedrag gerealiseerd worden.
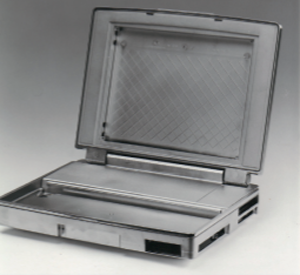
Chemische vernikkeling
Tenslotte bespreken we de chemische vernikkeling van magnesiumlegeringen, die onder de naam DNC-MG op de markt worden gebracht. DNC staat voor DURNI-COAT®. De chemische metallisering van magnesium en magnesiumlegeringen komt in beeld, wanneer naast een goed corrosiewerend gedrag, ook typische metallische eigenschappen zoals elektrische geleidbaarheid, warmteafvoer, glans, afscherming of soldeerbaarheid van het oppervlak vereist zijn. Chemische vernikkeling biedt daarvoor een veelvoud van voordelige eigenschappen, onder andere een hoge slijtvastheid, met name onder abrasieve belasting alsmede een gelijkmatige laagdikte, ook bij ‘lastig’ gevormde onderdelen. Een onontbeerlijke voorwaarde voor een goede weerstand tegen corrosie is een alzijdige en dichte coating; ‘chemisch nikkel’ waarborgt die. Chemisch vernikkeld worden in het algemeen spuitgietdelen (m.n. van de legeringen AZ91HP en AM50HP). Met het doel, het aantal voorbehandelingsstappen te verminderen en milieutechnisch verantwoorde elektrolyten aan te bieden, heeft AHC het DNC-proces verder ontwikkeld en met een speciale veredelingsvariant voor magnesiummaterialen aangevuld. Met DNC-MG is het thans mogelijk de metaallaag direct op het magnesium oppervlak aan te brengen. Het coatingproces verloopt als volgt: eerst vindt een uitwisselingsreactie plaats tussen het onedele basismateriaal en het nikkel. Is deze laag gesloten, dan wordt daarop de gebruikelijke autocatalytische nikkelfosforlaag opgebouwd.