Verspanend bewerken van aluminium en gelegeerd aluminium
Aluminiumlegeringen kunnen snel en economisch worden verspaand. Vanwege hun complexe metallurgische structuur, zijn hun verspaningskarakteristieken superieur aan die van zuiver aluminium.
Door: A.J. Schornagel
Ruimen
Ruimen is een methode om gaten te vergroten door het verwijderen van metaal met een enkel- en soms een meerpuntig snijgereedschap dat evenwijdig wordt voortbewogen met de rotatie-as van het werkstuk of gereedschap. Het ruimen van aluminiumlegeringen, en dan vooral de legeringen met een hoog siliciumgehalte, vereisen het gebruik van gereedschap met scherpe vrijloop- en stelhoeken. In het algemeen worden de vrijloophoeken groter genomen naarmate het siliciumgehalte lager is. Dezelfde gereedschapsgeometrie en snijgereedschap die wordt gebruikt voor het draaien van hoog-siliciumhoudende legeringen zoals 390, wordt ook toegepast voor het ruimen van deze legering.
Gereedschapsmateriaal
Hoewel snelstaalgereedschap tot op zekere hoogte wordt gebruikt voor het ruimen van aluminium, staat carbidegereedschap hogere oppervlaktesnelheden toe (tot 300 m/min of meer), met een opmerkelijk langere standtijd. Carbidesnijders halen makkelijk oppervlakteruwheden van 0,25 tot 0,50 ?m. In combinatie met precisieruimmachines, kunnen met diamantgereedschap oppervlakteruwheden worden gerealiseerd van 0,025 ?m. Dit gereedschap behoudt zijn vorm ook bij lange productiereeksen. Als de snede continu is en het metaal van het werkstuk bevat geen harde plekken, dan is diamantgereedschap het effectiefst voor het ruimen van de abrasieve hoog-siliciumlegeringen.
Beitelslijpen
Voor optimale standtijd dienen de snijkanten en aangrenzende oppervlakken vrij te zijn van bramen en krassen. Het met de hand slijpen op een oliesteen van de snijkanten wordt aanbevolen. Als een carbide ruimer wordt geslepen met een 400-500 grit diamantwiel, kunnen er oppervlakteruwheden van 0,075 tot 0,10 ?m worden bereikt.
Snelheid en aanzet
De optimum snelheid voor het ruimen van aluminiumlegeringen hangt enigszins af van de legering en warmtebehandeling, maar voor het grootste deel van het gereedschapsmateriaal en of de bewerking bestaat uit voor- of nabewerken. De keuze van de aanzet hangt eveneens grotendeels af van het gereedschapsmateriaal en of de bewerking bestaat uit voor- of nabewerken. Voor een ondiepere snede en lichtere aanzet wordt de snelheid hoger gekozen, ongeacht legering of gereedschapsmateriaal.
Snedediepte
De snedediepte is soms groter dan 2,5 mm voor voorruimen indien het vermogen dat ter beschikking staat groot genoeg is en de opstelling voldoende stijf kan worden gemaakt.
Snijvloeistof
Het gebruik van snijvloeistof wordt aanbevolen, maar er wordt ook wel droog geruimd. Als er geen gebruik wordt gemaakt van een snijvloeistof dan gaat dit ten koste van wat productiviteit, maatnauwkeurigheid, of oppervlakteafwerking. Een mengsel van 1 deel oplosbare olie op 20 tot 30 delen water wordt het vaakst gebruikt. Daarnaast wordt er vaak minerale olie, of minerale olie gemengd met tot 50% reuzelolie gebruikt, met name als de best haalbare oppervlakteafwerking wordt gewenst. Soms worden er mengsels van petroleum en smeerolie gebruikt.
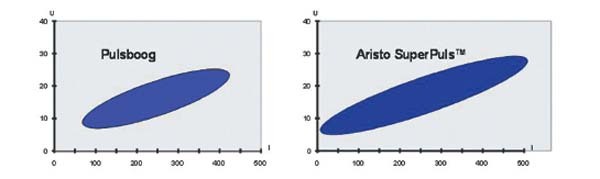
Schaven en sterke-armschaven
Schaven en sterke-armschaven leveren vlakke oppervlakken als gevolg van lineaire herhaalde beweging van een stilstaand werkstuk en een enkel-gepunt snijgereedschap.
Schaven
Zowel snelstaal- als carbidegereedschap voor het schaven van aluminium bezitten doorgaans een vrijloophoek van 30° of groter (soms wel 60°) en een zijdelingse vrijloophoek van 0°. Er wordt gewoonlijk een maximum snelheid aanbevolen van 90 m/min. Voorschaafaanzetten liggen rond 2,3 mm/slag als de snedediepte in de buurt van het aanbevolen maximum ligt van 13 mm. Als ondiepe sneden nodig zijn (als gevolg van onvoldoende vermogen of andere redenen) kan een sterkere aanzet worden gebruikt. Voor een snedediepte van 2,5 mm kan de aanzet worden vergroot tot ongeveer 3 mm/slag. Het naschaven van aluminiumlegeringen wordt gewoonlijk gedaan met een snede die niet dieper is dan 0,25 tot 0,40 mm en met een aanzet die gelijk is aan driekwart van de breedte van de nabewerkingsbeitel. Aluminiumlegeringen worden vaak geschaafd zonder snijvloeistof. Een snijvloeistof is behulpzaam bij het produceren van een betere oppervlakteafwerking, maar het overvloedig toevoeren van snijvloeistof is zelden mogelijk. Als oppervlakteafwerking het hoofddoel is, is het aanbrengen van een mengsel van petroleum en smeerolie, of van petroleum en reuzelolie, met een lap een gangbare procedure. Sproeien van snijvloeistof is effectief. Mengsels van oplosbare oliën worden veel gebruikt voor snijvloeistof-sproeisystemen.
Sterke-armschaven
Gereedschapsvormen, gereedschapsmateriaal en snijvloeistof voor het sterke-armschaven van aluminium zijn hetzelfde als die voor schaven. De maximum snelheid is doorgaans de maximum armsnelheid van de machine. Aanzet en snedediepte hangen ook in enige mate af van de machinecapaciteit. Een aanzet van 0,5 tot 0,75 mm/slag voor voorwerk en ongeveer 0,25 mm/slag voor nabewerking is normaal. De snedediepte bedraagt vaak 0,25 mm voor voorbewerken en 0,05 mm of minder voor nabewerken.
Brootsen
Brootsen is een verspaningsproces waarbij een snijgereedschap dat is voorzien van een groot aantal in de langsrichting gelegen snijkanten heen en weer wordt gehaald door een gat of over een oppervlak om metaal te verwijderen. Alle aluminiumlegeringen kunnen worden gebrootst met standaard brootsmachines en met dezelfde algemene procedures als voor andere metalen. Met de warmtebehandelbare aluminiumlegeringen worden echter betere resultaten behaald voor wat betreft oppervlakteafwerking. De principiële beperking bij het brootsen van aluminium is de moeilijkheid bij het handhaven van een accurate relatie tussen het gebrootste gat en andere oppervlakken van het werkstuk, zelfs als het begingat nauwkeurig is gelokaliseerd.
Gereedschapsmateriaal
Het voor algemene doeleinde gebruikte snelstaal, zoals M2, wordt gebruikt voor het merendeel van het gereedschap om aluminium mee te brootsen. Voor sommige hogeproductiebewerkingen, met name bij het brootsen van legeringen met een hoog siliciumgehalte, blijken brootsen die zijn gemaakt van het hoger gelegeerde snelstaal of van carbiden economisch te zijn. Oppervlaktebehandelingen zoals verchromen of anodiseren zijn behulpzaam bij het verlengen van de standtijd van snelstaal brootsen. Een fijne afwerking van het gereedschap kan van belang zijn. Bij een bepaalde toepassing kon de standtijd van de snelstaal broots worden verhoogd van 2000 tot 7400 stuks door de snijkanten nat te stralen met een superfijn schuurmiddel.
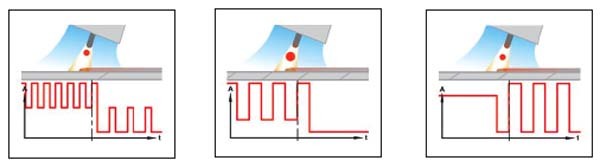
Brootsontwerp
Bij voorbrootsen is een grove tandsteek wenselijk, met op elk moment slechts twee of drie tanden in contact en snijdend. Voor inwendig nabrootsen worden de beste resultaten verkregen als slechts twee tanden snijden. Bij uitwendig nabrootsen moet de vrijloophoek 3,5° bedragen en voor inwendig brootsen 2°. Hoewel een grotere vrijloophoek een beter snijwerking geeft, bekort het de standtijd in aanzienlijke mate. De vrijloophoeken moeten dan ook tot een minimum worden beperkt om verlies van afmetingen te voorkomen als de broots wordt geslepen.
Snelheid en aanzet
Er wordt in het algemeen een snelheidsbereik van 10 tot 15 m/min voor het brootsen van aluminiumlegeringen aanbevolen. Als de stijfheid, toevoer van snijvloeistof en hardheid van het werkstuk nagenoeg ideaal zijn, kan het hogere deel van het bereik worden gebruikt. Als een of meer van deze condities minder dan ideaal is, moet de snelheid worden verlaagd. Voor het brootsen van aluminiumlegeringen wordt een grotere aanzet per tand aanbevolen dan voor het brootsen van staal. Een aanzet van 0,15 mm/tand is gewoonlijk het optimum voor spiebrootsen en ongeveer 0,8 mm/tand voor het brootsen van ronde gaten.
Snijvloeistof
Voor het behalen van de beste resultaten is het gebruik van snijvloeistof vereist. Overvloedige aanvoer van oplosbare olie gemengd met water is voor de meeste toepassingen voldoende. De oppervlakteruwheid wordt echter verbeterd door gebruik te maken van minerale olie, of minerale olie gemengd met reuzelolie.
Brootsen van hoog-siliciumhoudende legering 390
Horizontaal brootsen is lang de voorkeursmethode geweest voor voor- en nabrootsen van complexe gietijzeren werkstukken zoals cilinderkoppen en motorblokken. Met brootsen kunnen bij dergelijke werkstukken verscheidene oppervlakken tegelijk worden verspaand in exacte relatie met elkaar. Met brootsen is hoge metaalafname te realiseren en de omsteltijd van de machine is laag. Vanwege hun lage hardheid, elasticiteitsmodulus en sterkte worden aluminiumgietlegeringen van oudsher betiteld als ongeschikte kandidaten voor dit soort brootsbewerkingen De kenmerkende snijsnelheid voor een broots die is ontworpen voor het verspanen van gietijzer is laag (10 tot 50 m/min). De meeste aluminiumlegeringen gedragen zich rubberachtig bij zulke snelheden. Vanwege hun betrekkelijk lage hardheid verstoppen de spanen de snijtanden van de broots en het oppervlak van het gebrootste gietstuk vertoont uitbreken van materiaal en is ruw. De gereedschapskrachten die kenmerkend zijn voor zo’n broots, resulteren in breuk van de dunnere secties en randafbrokkeling bij andere secties. De lage elasticiteitsmodulus van de meeste aluminiumgietstukken, vergeleken met die van ijzer, stelt hoge eisen aan de opspanning.
Er is gebleken dat de legering 390 kan worden gebrootst met snijsnelheden en gereedschapsvormen die ook worden gebruikt voor het brootsen van gietijzer met carbidegereedschap. De standtijd van het gereedschap was veel hoger dan die bij gietijzer (afbeelding 1). Het is tevens duidelijk dat oppervlakteruwheden van minder dan 2,50 ?m kunnen worden verkregen zolang de spaandikte van elke snijkant onder 0,10 mm kan worden gehouden (afbeelding 2). Zulke spaanbelastingen zijn kenmerkend voor het nabrootsen van gietijzer en de oppervlakteruwheid die wordt verkregen is vergelijkbaar met of zelfs beter dan die welke wordt verkregen bij gietijzer. Het gebruik van een koelmiddel heeft weinig invloed op de standtijd of oppervlakteruwheid, maar kan wel behulpzaam zijn bij de spaanafvoer. Proeven hebben uitgewezen dat variatie van de spaanhoeken, vrijloophoeken en spaanbelasting effectief kan zijn bij het reduceren van de snijkrachten tijdens brootsen. Deze benadering van lage snijkrachten is niet beslist noodzakelijk voor legering 390, omdat de snijkrachten lager zijn dan de helft van die voor gietijzer bij vergelijkbare voorbrootsbewerkingen met negatieve spaanhoeken.
Boren met boormachines
Boren is een proces waarbij gaten worden gemaakt door middel van het gebruik van een roterend eindsnijgereedschap met een of meer snijlippen en een of meer spiraalvormige groeven of buizen voor het uitwerpen van de spanen en voor de passage van snijvloeistof. Hoewel de standaard spiraalboren en boorapparatuur die wordt gebruikt voor staal ook kunnen worden gebruikt voor het boren van aluminiumlegeringen, vereisen optimale resultaten boren van een speciaal ontwerp alsmede hogere rotatiesnelheden en zwaardere aanzetten. Boren voor aluminium worden gewoonlijk gemaakt met diepe, goed gepolijste groeven, nauwe intervallen en grote spiraalhoeken. Een correct boorontwerp en boorpraktijk voorzien in een drie tot vier maal grotere hoeveelheid te verwijderen metaal als die voor staal per eenheid van vermogen. Voor het boren met boormachines moet de spiraalhoek van de boor worden vergroot met de diepte van het te boren gat, reikend van een lage spiraalhoek van 24° voor zeer ondiepe gaten in dun materiaal tot een hoge spiraalhoek van 40 tot 48° voor diepe gaten, waarbij vrijer snijden belangrijk is. De boren met grote spiraalhoek hebben een scherpere snijhoek, hetgeen resulteert in verminderde wrijving en schoner snijden. Geleidingsrand en hulpvrijloopvlak zijn smaller dan bij de boor met lage spiraalhoek, hetgeen resulteert in verminderde wrijving en meer spaanruimte in de groeven. De iets hogere weerstand van de spaanafvoer kan worden overwonnen door de groeven te polijsten en wat snijvloeistof toe te voeren. Dit type boor wordt aanbevolen voor diepe gaten, maar is ongeschikt voor het boren in dun materiaal vanwege zijn neiging om te buigen. Een spiraalboor met een spiraalhoek van 28° is geschikt voor gaten van middelmatige diepte tot ongeveer zes maal de boordiameter. Een boor met een spiraalhoek van 24° of lager wordt aanbevolen voor dunwandig werk omdat hij minder neigt tot overaanzet. De punthoek van standaard spiraalboren ligt tussen 116 en 118°. Voor het boren van de meeste aluminiumlegeringen moet de hoek 130 tot 140° bedragen om vlotte spaanafvoer te verzekeren en om braamvorming tot een minimum te beperken. Boren voor legeringen met een hoog siliciumgehalte moeten echter zijn voorzien van een minder stompe punt, zo’n 90°, voor gemak van penetratie. Voor het boren van dunne plaat moet de punthoek zeer stomp zijn om de boor gelegenheid te geven om over zijn volledige diameter te boren voordat hij doorbreekt. Met dit type boor kan een steun nodig zijn bij het centreren. De standaard lipvrijloop van 12 tot 13° moet worden verhoogd tot ongeveer 17° voor zware aanzetten en voor zachtere legeringen. Onvoldoende lipvrijloop zal excessieve boorbreuk veroorzaken. De snijlippen van de boor moeten scherp en glad zijn en alle oppervlakken waarover de spaan glijdt moeten worden gepolijst voor minimale wrijving en spaanopbouw.
Boormateriaal
De meeste boren voor aluminium zijn gemaakt van snelstaal. M1, M7 en M10 zijn de meest voorkomende typen. Alleen heel af en toe is het mogelijk om de bijkomende kosten voor boren die zijn gemaakt van een hoger gelegeerd snelstaaltype of carbide voor gebruik in boormachines voor conventioneel boorwerk te rechtvaardigen.
Snelheid en aanzet
Met de meeste boormachines is de omtreksnelheid van boren met kleine diameter betrekkelijk laag, daarom kunnen zulke boren worden bedreven bij de maximum efficiënte rotatiesnelheid van de machine. In het algemeen geldt dat boren van snelstaal kunnen worden gebruikt tot een maximum snelheid van ongeveer 180m/min. Als variabele snelheid mogelijk is, kan bij het boren van diepere gaten de standtijd worden verlengd door de boor geleidelijk op snelheid te brengen. Vanwege het gemak waarmee de meeste aluminiumlegeringen kunnen worden gepenetreerd, kunnen er aanzetten worden gebruikt tot het dubbele van de waarde voor het boren van staal. De aanzet varieert met de boordiameter. De boren met grotere diameters staan zwaarder aanzetten toe. Het boren van dunwandig materiaal vereist geen gebruik van snijvloeistof, maar het is essentieel voor de standtijd van de boor en de kwaliteit van het geboorde gat dat er een ruime hoeveelheid snijvloeistof wordt gebruikt bij het boren van alle diepe gaten. Oplosbare olie-emulsies of -mengsels van petroleum en reuzelolie voldoen voor algemeen boorwerk. Bij het boren van gaten dieper dan zes maal de boordiameter moet het werkstuk worden gekoeld door middel van sproeien. Daar komt bij dat de boor tijdens het boren verscheidene malen moet worden teruggetrokken om er zeker van te zijn dat het gat volledig wordt gevuld met snijvloeistof.
Diepboren
Kanonboren, voorzien van een punt van hetzij carbide hetzij snelstaal, hebben voor tal van diepboortoepassingen het gebruik van spiraalboren verdrongen, ongeacht het te boren materiaal. Bij kanonboren hangt de maximum diepte die kan worden geboord in het algemeen af van de boorgrootte. Kanonboren met een enkelgroefsnijkop en gegroefde flank moeten van voldoende snijvloeistof onder hoge druk worden voorzien op de plaats waar de snijkant contact maakt met het werkstuk. Dit houdt de snijkant koel en verzekert dat de spanen worden afgevoerd via de spaanafvoergroef. Snijvloeistof wordt in het algemeen toegevoerd onder een druk van 3,5 tot 4,0 MPa voor boren tot een diameter van 9,5 mm of kleiner en van 2 tot 3 MPa voor grotere boordiameters. Een pomp met een vermogen van 4 kW is doorgaans nodig voor middelmatige toepassingen. Een olie op basis van paraffine met een viscositeit van 100 tot 125 SUS bij 40°C wordt met succes gebruikt voor het kanonboren van aluminium met een 9,5 mm diameter boor, bij een snelheid van 90 m/min voor snelstaal of 180 m/min voor carbide en met aanzetten van 0,025 tot 0,08 mm/omw. Hoewel diepboorproblemen tot op zekere hoogte zijn opgelost door de ontwikkeling van kanonboren en speciale boorapparatuur, is deze apparatuur kostbaar en het gebruik valt niet altijd te rechtvaardigen.